In-Mold Labeling (IML Injection Molding)
In-mold labeling also known as IML injection molding is one of the IMD processes. IML only refers to put the pre-printed label inside the mold cavity, and then inject or blow the resin material over it. After this process, the label and the plastic molded part will become one combined component. This technique is widely used in the packaging industry. The main characteristic of IML is the label is located on the same surface as the plastic part. It replaces the traditional label pasting machine, lowers down the cost, and increases the package’s recoverability rate.
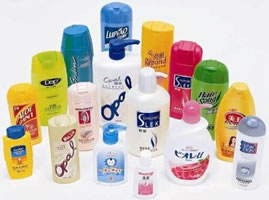
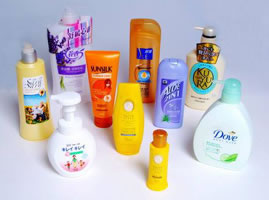
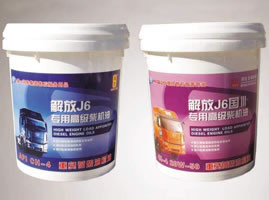
Advantages of In-Mold Labeling
Product appearance is nice and attractive:
The products made by IML injection molding process are contour artistic, have a smooth feeling when touching the surface, and the picture is exquisite, so it can achieve a very good visual expression. The label is closely integrated with the bottle with good adhesiveness allover the label area. In addition, the label is able to avoid the touch, scratch and contamination might caused in the process of production and transportation. The durability is long, and it will not be affected by the wet environment or gets moldy. Especially suitable for the labels and packaging appearance to demand higher commodity and cosmetics industry.
Anti-counterfeiting Function:
In-mold labeling process is relatively more complex and needs the special processing tools. So there are some technical barriers and hard to counterfeit or imitation. So it will effectively reduce the possibility of fraud, provide a reliable means of brand protection.
Safety and Environmental Friendly:
Traditional labeling method needs to mold the plastic part first and then paste the label onto it afterwards. While IML injection molding method only needs one single process to have the labels attached to the plastic parts. This avoids the potential pollution to the plastic parts during the traditional labeling process. IML injection molding normally uses the same material for the label and the molded plastic parts, therefore, this makes the recycle job for this type of product easier and more efficiently, and so that reduces the cost.
High Efficiency and Cost-effectiveness:
There is only one process for in-mold labeling, no secondary process afterwards. This makes the manufacturing progress shorter and reduce the stock levels. And it largely reduces the production cycle time, increases the efficiency and reduces the labor cost. In addition, In-mold labeling has a better printing performance, it can achieve the same elegant pattern looking as the adhesive labels.