Rotational Molding Service
Rotational molding’s working principle is to put the powder resin into the cold mold, rotate and heat the mold at the same time, so that the powder resin will melt and apply to the entire mold cavity evenly. Finally, cool down the mold and then get the molded products. Common products made by rotational molding process include: Containers, Shield Covers, Lighting Shells, Furniture, Plastic Boat, Sporting Equipment, Bath, Public Toilet, Telephone Booth, Children Playground Equipment, Advertisement Show Board, Water Float, and so on. Maxtech custom rotational molded products based on client’s unique design, we can also improve the design to reduce the cost and better fit the using purpose.
Production Equipment List of Plastic Rotational Molding Equipment:360 degree shuttle rotomolding machine | 2 sets |
Heating swing rotomolding machine | 4 sets |
Multiple arms and stations rotomolding machine | 8 sets |
360 degree all around tower type rotomolding machine | 2 sets |
Shuttle swing rotomolding machine | 2 sets |
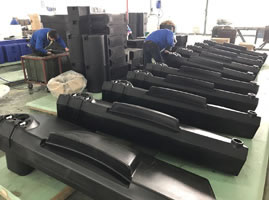
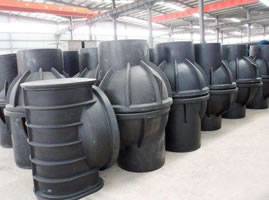
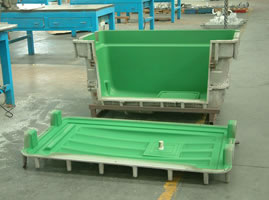
Product Range: Maximum size is 4200mm*4200mm
Molded Wall-Thickness: 2mm ~ 16mm
Tolerance Range: ±3mm per meter
Surface Treatment: Color can be custom made, please let us know the Pantone color code before production.
Quality Control:
Quality inspection will be performed strictly under ISO9001:2008 management standard.
Inspection tools are including: Projector, CMM, Chromatographic Instrument, Abrasion Tester.
Characteristic for Rotational Molding Process:
1. Low mold cost: for one same product, rotational mold cost will only be 1/4 or 1/3 of injection mold cost.
2. Better strength at the edges of rotational molded parts. It can give a 5mm thickness at the edges, this will solve the weak edge problem of hollow products completely.
3. Large scale of wall-thickness, can be as thin as 2mm to as thick as 16mm.
4. Can molded in large size products, almost no upper limits in size.
5. Can molded complex shapes which cannot be made by other plastic molding processes.
6. Rotational molding can make completely enclosed products.
7. Foaming can be added into the rotational molded parts to reach thermal insulation purpose.
8. Even wall-thickness, no wasted flash materials, seamless.
Applications for Rotational Molding Process:
1. Containers: water tanks, oil tanks, transportation containers, dumpsters, shield covers, chemical tanks, reaction tanks.
2. Automobile industry: automobile fittings, air-conditioning pipes, back of chairs, armrests.
3. Sports equipment: snowboards, yachts, water float balls, bicycle seats, surfboards, boats, buoys, dock bumpers.
4. Children toys: children slides, desks and chairs, climbing wall, soft playgrounds.